ITER (International Thermonuclear Experimental Reactor) is the most ambitious contemporary scientific project in the field of energy. It aims to demonstrate that thermonuclear fusion is a sustainable, non-CO2 emitting, industrialisable energy source that can be used to replace exhaustible fossil fuels such as natural gas or oil.
Project Summary
Located in Saint-Paul-lez-Durance, near Aix-en-Provence, ITER Organization manages the design and construction of the world’s largest Tokamak after more than 30 years of research.
Initiated at the 1985 Geneva Super-Power Summit, the ITER programme is governed by an international agreement ratified by the ministers of the ITER member entities, namely between Japan, the United States, India, Russia, China, Korea and the European Union (Euratom).
The contribution of ITER members is mainly made “in kind” through “domestic agencies” responsible for the manufacture and delivery of machine parts and installation systems. Technical cooperation agreements have also been signed with Australia and Kazakhstan.
This vast international scientific programme covers 180 hectares of Provençal land and represents a budget of 16 billion euros. Site servicing work began in 2017 and construction of the facility’s buildings (39 in total) was launched in August 2010. The synergy between the assembly sites of the machine will allow, according to forecasts, to produce a first plasma in December 2025.
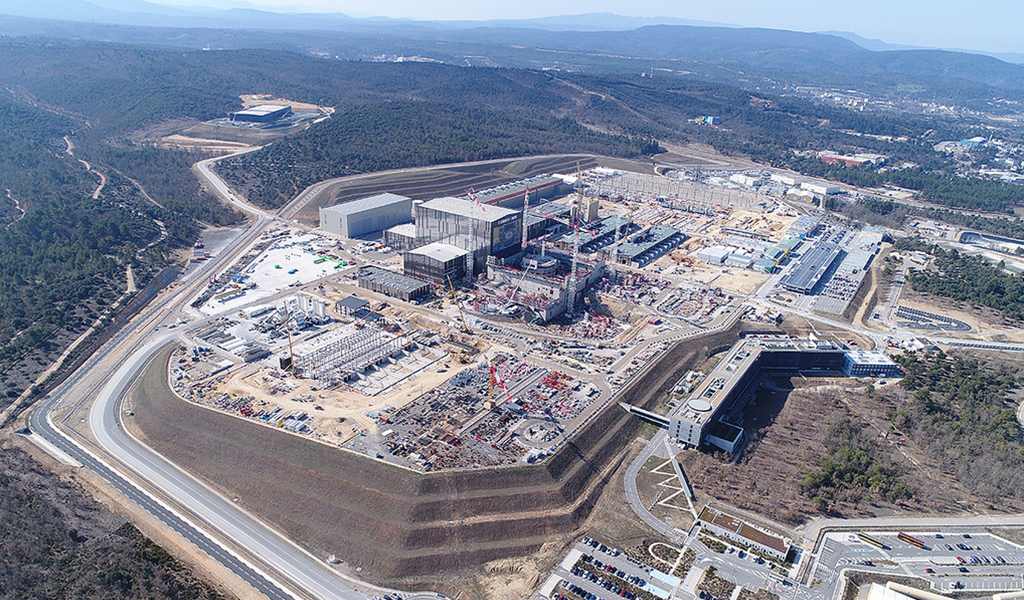
Full Case Study
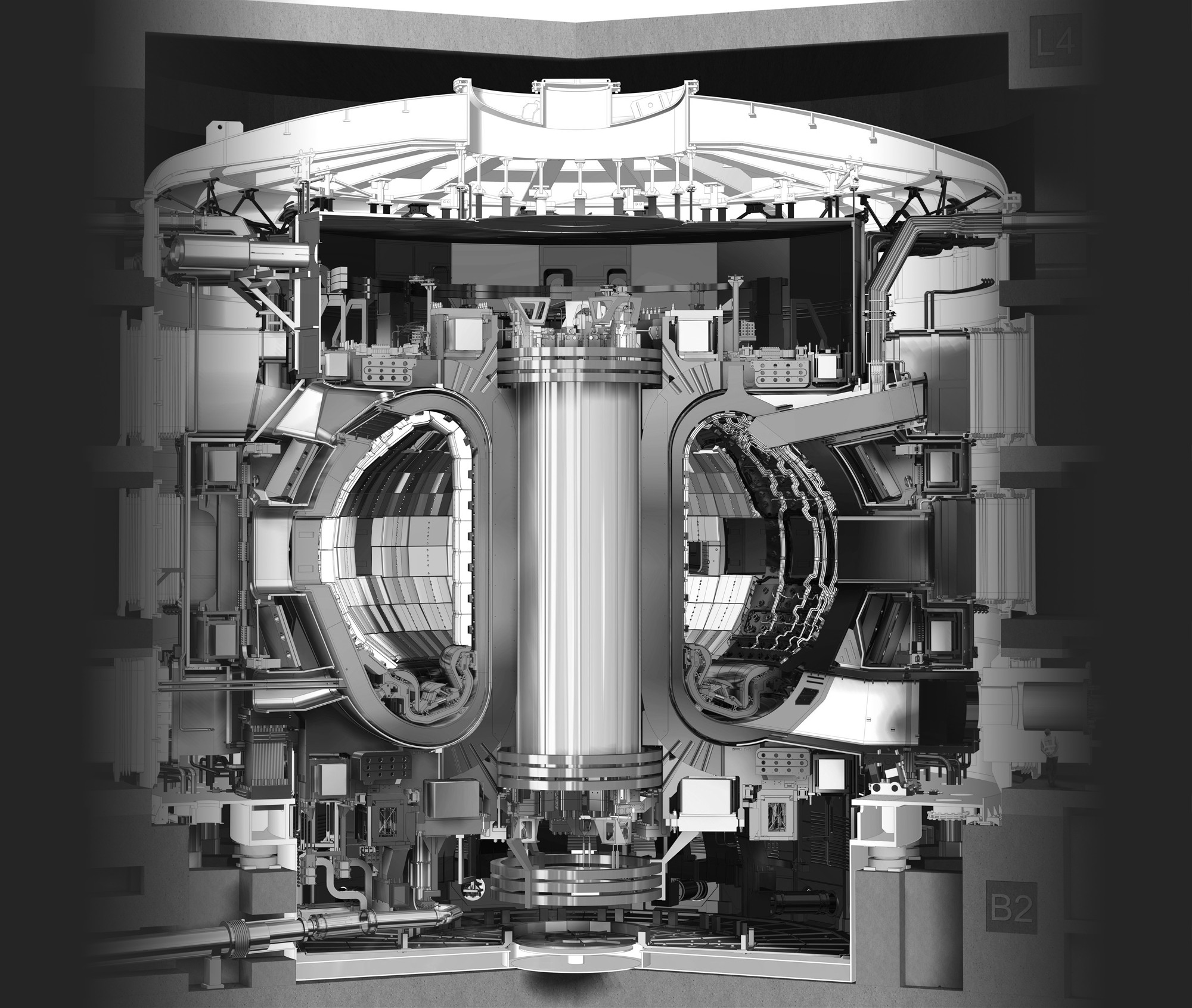
Complex and unusual, the largest Tokamak ever designed is an experimental machine designed to harness the energy of fusion. In the enclosure of a tokamak, the energy generated by the fusion of atomic nuclei is absorbed in the form of heat. In the “vacuum chamber” of the machine, the plasma is heated to 150 million degrees Celsius, 10 times the temperature at the heart of our sun.
The Tokamak ITER incorporates multiple elements, such as the 10,000 tonnes of superconducting magnets designed to provide a magnetic field capable of confining and keeping the plasma away from the walls of the vacuum chamber. To do this, not only magnets but also vacuum pumps and other ancillary systems must be maintained at a temperature close to absolute zero. The related cryogenic technologies are a major condition for the success of the project. ITER’s cryogenic system will be the most powerful ever built.
Design Goals
Specific constraints such as anti-seismic devices or structural waterproofing are inherent components of a nuclear fusion project. For the construction companies involved in the project, these are real performance challenges.
The construction of the Tokamak complex on seven levels in the heart of the site; the assembly building as well as those of the auxiliary buildings, such as the HVAC zone or the cold plant, are planned between 2014 and 2021. These priority structures are all essential for the production of the first ITER plasma. More than 70% of civil engineering is now completed.
Buildings 51 and 52 (Cryoplant compressor building and Cryoplant coldbox building) of the science complex make up the cryogenic plant adjacent to Tokamak. Covering an area of 8,000 m², this auxiliary zone is intended to produce the fluids required to cool the components (superconducting magnets, heat shields and cryo-pumps) of the Tokamak via a network of cold lines, the cryolines.
In addition to the extremely advanced design and unprecedented size of the Cryoplant, the structure of the entire building complex also had to integrate materials and construction processes designed to enhance the performance of the facilities they house.
During the design phase, ENIA Architects in charge of the architectural cladding of the ITER installation wanted the facades to reflect “the precision of the research work carried out inside the buildings“. The specifications produced in collaboration with the Engage, civil engineering consortium, specify that the design of the cladding should guarantee a specifically clean environment inside the buildings.
To enable this alliance, the members of the project team have selected experienced craftsmen and construction professionals.
Results
In response to the specificities of nuclear and architectural civil engineering imposed by the prime contractors, a cladding composed of multiple layers of cladding was installed on the buildings.
Specialized in waterproofing and cladding, it is the B2F company based in Aubagne that was chosen for its expertise in metalwork and façade waterproofing. Among the various insulating layers and the final envelope of steel alternately polished and lacquered, the company also installed 52.3m² of louvers model B5157, designed by Construction Specialties and prescribed upstream by the project management.
Extruded in high quality aluminium, the B5157 architectural ventilation grilles are composed of upper, lower and lateral posts and horizontal slats. They form a unique and interdependent unit that is easy and quick to install, thanks to a ready-to-install implementation system.
The special rafter cut-out of the B5157 profiles ensures an optimal air flow without letting rain in. Aluminium folds finish off each end of the blades to drain off any water residue. To preserve the clean environment, the louvers have been fitted with anti-pest shut-off grids.
Manufactured in France and tested according to the AMCA (Air Movement and Control Association International) protocol, the specifications of the B5157 grilles are certified by this label of high airflow requirements.
This accreditation ensures the project management that the Construction Specialties construction grids implemented for the ITER project provide efficient ventilation and properties in line with the ambition of the ITER project.
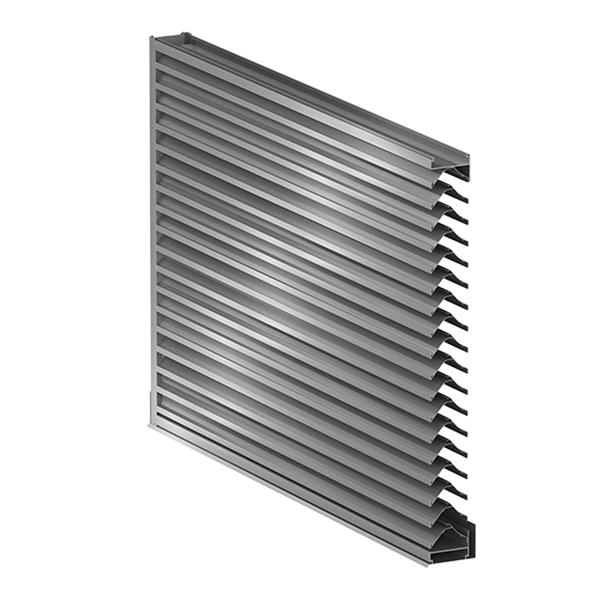
We would like to thank Iter Organization for allowing us to use the photos that illustrate this article.
Credit © ITER Organization, http://www.iter.org/